,allowExpansion)
Digital Twins for
The Intelligent Factory
Digital Twins
The introduction of intelligent processes drives the digital transformation of the manufacturing industry with a multitude of optimisation possibilities, production processes are becoming increasingly digital and automated. Now it is important for companies to make the best possible use of the potential of technological developments such as IoT, cloud computing and machine learning in order to remain competitive. And this is the starting point for the Digital Twins concept.
Real-time data from connected objects generate a digital footprint. This data can be processed, aggregated and evaluated according to various criteria and creates a digital profile of the product, which allows the physical properties of a factory, product or process to be mapped - the so-called Digital Twin.
The Tasks of Digital Twins
in Smart Factories
Industry 4.0 has ushered in the transition from purely physical systems to cyber-physical systems: Production facilities are becoming increasingly intelligent, and the much-cited Smart Factory is being created. In this context, we encounter the Digital Twin as the exact digital representation of a physical system.
A digital twin ultimately thrives on the rapid collection, aggregation and analysis of data from connected technologies and allows the simulation of possible scenarios for predicting results in the virtual world without affecting production. This not only saves valuable time, but also helps to identify possible errors with a predictive strategy before it is transferred to the physical processes. This has a positive effect on process efficiency and product quality.
Support or services are also accelerated and streamlined if machines can be supplied with the necessary software or configuration updates remotely, for example via a wireless connection.
A central strength of the Digital Twin lies in the visualisation of the data: data thus becomes insights into the processes, which are accessible not only to experts but also to a technically less experienced audience and are also spatially independent. This data visualization promotes learning and decision-making processes at all levels of the Connected Enterprise and helps to identify critical areas directly.
Metal 3D Printing for The Automotive Sector: Project IDAM
Concept Reply has already successfully developed and implemented Digital Twins for different scenarios and in different industries. The IoT expert of the Reply Group is currently responsible for the creation of a Digital Twin for an entire additive manufacturing production chain within the framework of the BMBF research project "Industrialization and digitization of additive manufacturing for automotive series processes" (IDAM). The aim of the project is to use metal 3D printing for the serial production of automotive parts.
The development of a Digital Twin is of central importance in this project. Additive manufacturing can only be seamlessly integrated into an automotive production environment by converting to a highly automated series process, integrating the software landscape and connecting to the conventional production line.
On the physical side, all links in the process chain must be equipped with suitable sensors (e.g. heat, pressure, vibration and visual sensors). Via precisely defined interfaces and protocols, these sensors safely and reliably deliver the data that make up the Digital Twin. Conversely, actuators are used at suitable points to transmit instructions from the Digital Twin to the physical world.
The Digital Twin thus becomes a hub for all data analysis and visualization tools to facilitate communication between machines and relevant stakeholders. It also opens up the possibility of integrating developments from the fields of big data and artificial intelligence with the aim of orchestrating the highly complex interaction between different machines in the entire production environment.
The Role of Digital Twins in The Smart Factory
Concept Reply has already implemented several digital twin projects in the automotive industry: For example, a digital twin was used to model the technical features of hardware and software for different vehicle models, model series and configurations. Concept Reply automated the data collection process according to the desired platform in order to harmonize the various data models. This enables Data Scientists to access specific data points, such as vehicle speed, without having to know the technical details of the target platform.
In the Connected Infrastructure area, a Device Shadow was developed for devices for which a connection is not continuously guaranteed. The devices run on battery power and their state is managed in the cloud. In this way, customers are able to ensure synchronisation between the desired and actual state of the device and update the state of the device when necessary.
In an industry 4.0 related project Concept Reply has developed a monitoring system for a plant fleet in a factory. The customer is now able to track a number of KPIs, the most important of which is Overall Equipment Effectiveness (OEE). The OEE describes how well a machine is utilized in relation to its capacity. A bad OEE is a clear signal that measures such as machine maintenance or process optimization are required. In addition, the alarm log files provide a starting point to uncover technical deficits of the machines in terms of process mining, and to train with machine learning alarm patterns, which help to further improve performance.
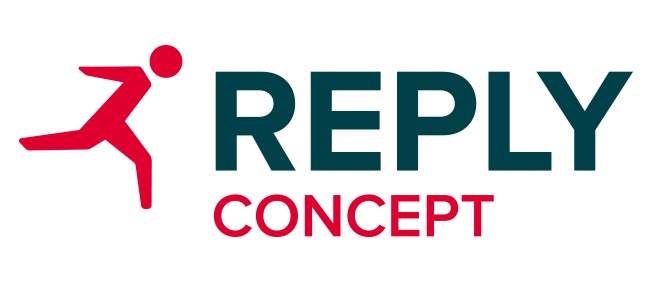
Concept Reply is an IoT software developer specializing in the research, development and validation of innovative solutions and supports its customers in the automotive, manufacturing, smart infrastructure and other industries in all matters relating to the Internet of Things (IoT) and cloud computing. The goal is to offer end-to-end solutions along the entire value chain: from the definition of an IoT strategy, through testing and quality assurance, to the implementation of a concrete solution.