,allowExpansion)
Digital Twins für die intelligente Fabrik
Digitale Zwillinge
Die Einführung intelligenter Prozesse treibt die digitale Transformation des verarbeitenden Gewerbes mit einer Fülle an Optimierungsmöglichkeiten voran, Fertigungsprozesse werden immer digitaler und automatisierter. Nun gilt es für Unternehmen, das Potenzial technologischer Entwicklungen wie IoT, Cloud Computing und Machine Learning bestmöglich für sich zu nutzen, um wettbewerbsfähig zu bleiben. Und hier liegt der Ansatzpunkt für das Konzept des Digital Twins.
Echtzeitdaten von vernetzten Objekten, erzeugen einen digitalen Fußabdruck. Diese Daten können nach verschiedenen Kriterien verarbeitet, aggregiert und ausgewertet werden und lassen ein digitales Profil des Produktes entstehen, was eine Abbildung der physikalischen Eigenschaften einer Fabrik, eines Produkts oder eines Prozesses ermöglicht - den sogenannten Digital Twin.
Die Aufgabe der Digital Twins in der Smart Factory
Die Industrie 4.0 hat den Übergang von rein physikalischen Systemen hin zu cyber-physischen Systemen eingeläutet: Produktionsstätten werden zunehmend intelligent, die viel zitierte Smart Factory entsteht. In diesem Kontext begegnet uns der Digital Twin als die exakte digitale Abbildung eines physikalischen Systems.
Ein Digital Twin lebt letztlich von der schnellen Erfassung, der Aggregation und der Analyse der Daten vernetzter Technologien und erlaubt die Simulation möglicher Szenarien zur Vorhersage von Ergebnissen im Virtuellen, ohne dass dabei die Produktion beeinträchtigt wird. Das spart nicht nur wertvolle Zeit, sondern hilft dabei, mögliche Fehler mit einer prädiktiven Strategie zu identifizieren, bevor sie auf die physischen Prozesse übertragen wird. Dies wirkt sich positiv auf Prozesseffizienz und Produktqualität aus.
Auch Support oder Servicedienste werden beschleunigt und verschlankt, wenn Maschinen bei Bedarf remote, etwa über eine kabellose Verbindung, mit den nötigen Software- oder Konfigurationsupdates versorgt werden können.
Eine zentrale Stärke des Digital Twin liegt in der Visualisierung der Daten: aus Daten werden so Einsichten in die Abläufe, die sich neben den Fachleuten auch einem technisch weniger versierten Publikum erschließen und zudem räumlich unabhängig verfügbar sind. Diese Datenvisualisierung fördert Lern- und Entscheidungsprozesse auf allen Ebenen der Connected Enterprise und hilft kritische Bereiche unmittelbar zu identifizieren.
Metall 3D-Druck für die Automobilindustrie: Projekt IDAM
Concept Reply hat bereits erfolgreich Digital Twins für verschiedene Szenarien und in unterschiedlichen Branchen entwickelt und implementiert. Aktuell ist der IoT-Experte der Reply Gruppe im Rahmen des BMBF-Forschungsprojektes „Industrialisierung und Digitalisierung von Additive Manufacturing für automobile Serienprozesse" (IDAM) für die Erstellung eines Digital Twin einer gesamten Additive-Manufacturing-Produktionskette verantwortlich. Das Projekt verfolgt das Ziel, den Metall-3D-Druck für die Serienproduktion von Automobilteilen einzusetzen.
Der Entwicklung eines Digital Twin kommt in diesem Projekt eine zentrale Bedeutung zu. Nur durch die Wandlung hin zu einem hochautomatisierten Serienprozess, die Integration der Softwarelandschaft und die Anbindung an die konventionelle Fertigungslinie, lässt sich Additive Manufacturing nahtlos in eine automobile Produktionsumgebung einbinden.
Auf der physischen Seite müssen dazu alle Glieder der Prozesskette mit geeigneten Sensoren (z.B. Wärme-, Druck-, Vibrations- und visuelle Sensoren) ausgestattet sein. Diese Sensoren liefern über genau definierte Schnittstellen und Protokolle sicher und zuverlässig eben jene Daten, aus denen der Digital Twin besteht. Umgekehrt werden an geeigneten Stellen Aktuatoren eingesetzt, um Anweisungen des Digital Twin in die physische Welt zu übertragen.
Der Digital Twin wird so zu einer Drehscheibe für alle Datenanalyse- und Visualisierungswerkzeuge, um die Kommunikation zwischen Maschinen und den relevanten Stakeholdern zu erleichtern. Er eröffnet zudem die Möglichkeit, Entwicklungen aus den Bereichen Big Data und Künstliche Intelligenz einzubinden, mit dem Ziel, das hochkomplexe Zusammenspiel zwischen verschiedenen Maschinen in der gesamten Produktionsumgebung zu orchestrieren.
Die Aufgabe der Digital Twins in der Smart Factory
Concept Reply hat bereits mehrere Digital-Twin-Projekte in der Automobilindustrie umgesetzt: Beispielsweise wurde ein digitaler Zwilling zur Modellierung der technischen Besonderheiten von Hard- und Software bei unterschiedlichen Fahrzeugmodellen, Baureihen und Konfigurationen eingesetzt. Dabei hat Concept Reply den Prozess der Datenerfassung je nach gewünschter Plattform automatisiert, um die verschiedenen Datenmodelle zu harmonisieren. So können Data Scientists auf bestimmte Datenpunkte, wie etwa die Fahrzeuggeschwindigkeit zugreifen, ohne die technischen Details der Zielplattform kennen zu müssen.
Im Bereich Connected Infrastructure wurde ein Device Shadow für Geräte entwickelt, bei denen eine Verbindung nicht durchgehend gewährleistet ist. Die Geräte laufen mit Akkubetrieb und ihr Zustand wird in der Cloud verwaltet. Auf diese Weise sind Kunden in der Lage, die Synchronisation zwischen dem gewünschten und dem tatsächlichen Zustand des Gerätes sicherzustellen und bei Bedarf den Zustand des Gerätes zu aktualisieren.
In einem Industrie-4.0-bezogenen Projekt hat Concept Reply ein Überwachungssystem für eine Anlagenflotte in einer Fabrik entwickelt. Dank individueller Signal-Sensoren, Alarmprotokollen und komplexer Zustandsmaschinen ist der Kunde heute in der Lage, eine Reihe von KPIs zu verfolgen; die wichtigste davon ist die Overall Equipment Effectiveness (OEE). Die OEE beschreibt, wie gut eine Maschine im Verhältnis zu ihrer Kapazität ausgelastet ist. Eine schlechte OEE ist ein klares Signal dafür, dass Maßnahmen wie Maschinenwartung oder Prozessoptimierung erforderlich sind. Darüber hinaus bieten die Alarm-Logdateien einen Ansatzpunkt, um im Sinne eines Process Mining technische Defizite der Maschinen aufzudecken, und mit Machine Learning Alarmmuster zu trainieren, die helfen die Leistung weiter zu verbessern.
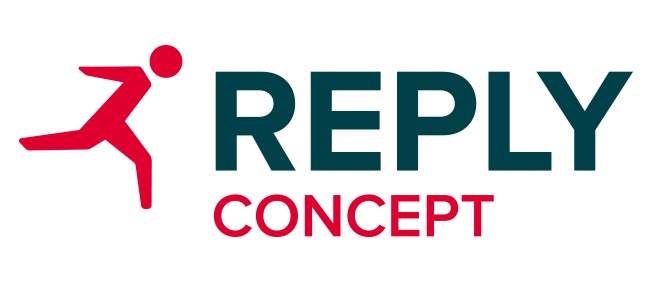
Concept Reply ist ein auf die Erforschung, Entwicklung und Validierung innovativer Lösungen spezialisierter IoT-Softwareentwickler und unterstützt seine Kunden aus der Automobil-, Fertigungs- und Smart-Infrastructure-Industrie sowie anderen Branchen in allen Fragen rund um das Internet der Dinge (IoT) und Cloud Computing. Ziel ist es, End-to-End-Lösungen entlang der gesamten Wertschöpfungskette anzubieten: von der Definition einer IoT-Strategie über Testing und Qualitätssicherung bis hin zur Umsetzung einer konkreten Lösung.